  |
3.6 Steps in Selecting a Control Valve |
The basic steps in
control valve selection are presented below.
- The first step in control valve selection involves
collecting all relevant data and completing the ISA Form
S20.50. The piping size must be set prior to valve sizing,
and determining the supply pressure may require specifying a
pump. The novice might have to iterate on the needed piping,
pump pressure and pressure drop through the piping network.
- Next, the size of the valve is required; select the
smallest valve Cv that satisfies the maximum Cv
requirement at 90% opening. While performing
these calculations, checks should be made regarding flashing,
cavitation, sonic flow and Reynolds number to ensure that the proper
equation and correction factors are used. As many
difficulties occur due to oversized valves as to undersized
valves. Adding lots of “safety factors”
will result in a valve that is nearly closed during normal operation
and has poor rangeability.
- The trim characteristic is selected to provide good
performance; goals are usually linear control loop behavior along with
acceptable rangeability.
- The valve body can be selected based on the features in
Table 5 and the typical availability in Table 6. Note that
the valve size is either equal to the pipe size or slightly less, for
example, a 3-inch pipe with a 2-inch globe valve
body. When the valve size is smaller than the
process piping, an inlet reducer and outlet expander are required to
make connections to the process piping.
- The actuator is now selected to provide sufficient force to
position the stem and plug.
- Finally, auxiliaries can be added to enhance
performance. A booster can be increase the volume of the
pneumatic signal for long pneumatic lines and large
actuators. A positioner can be applied for slow feedback
loops with large valves or valves with high actuator force or
friction. A hand wheel is needed if manual operation of the
valve is expected.
Table 6. Information
on Standard Commercial Control Valves1
Body
Type
|
Size
(in)
|
Maximum
Pressure (psia)2
|
Temperature
(°F )
|
Capacity3
Cd = Cv/d2
|
Globe
|
1/4 to 16
|
50,000
|
cryogenic
to 1200
|
10
|
Ball
|
1/2 to 36
|
2500
|
up to
1400
|
30
|
Butterfly
|
3/4 to
200
|
2500
|
cryogenic
to -2200
|
20
|
Diaphragm
|
1/4 to 20
|
100
|
-30 to
2200
|
22
|
- Compiled from Andrew and Williams (1980) and Driskell
(1983)
- Higher pressures for smaller sizes and moderate
temperatures.
- The parameter d is the valve connection diameter in inches.
For an
introductory discussion for matching valve body to application, select
this button to be directed to a site on the WWW. |
|
For additional
information on valve selection and sizing. See Chapter 5 in this
resource. |
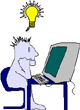 |